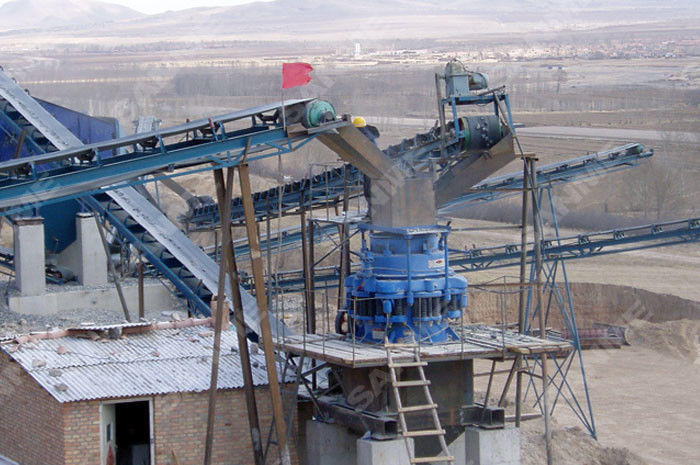
400Kw Metallurgy Feeding 460mm Cone Crusher Machine
Minimum Order Quantity: | Negotiate | Price | Negotiate |
---|---|---|---|
Packaging Details | Standard container, spare parts will be packed in wooden cases | Delivery Time | 2 months |
Payment Terms: | T/T, L/C | Supply Ability | 50 sets per Month |
Place of Origin: | Shanghai, China | Brand Name: | SANME | |
---|---|---|---|---|
Certification: | ISO&CE | Model Number: | SMS Cone crusher, VC sand making machine, XL sand washer, ZSW vibrating feeder, YK vibrating screen | ">SMS Cone crusher, VC sand making machine, XL sand washer, ZSW vibrating feeder, YK vibrating screen |
Detail Information |
|||
Raw Materials: | River Pebbles | EQUIPMENTS: | Cone Crusher, Sand Making Machine, Sand Washer, Vibrating Feeder, Vibrating Screen |
---|---|---|---|
Application: | : Construction Works , Energy & Mining | Core Components: | PLC, Bearing, Gearbox, Motor |
After-sales Service: | Online Support, Service Machinery Overseas | Warranty Of Core Components: | 1 Year |
High Light: |
PLC River Pebble Stone Crushing Machine,ISO Coarse Stone Crushing Machine,Screening Coarse Stone Crushing Machine |
Product Description
complete river pebble production line
River stons are hard-earned stones with various colors. They are the main material for mining yellow sand. They can also be used in many industries such as architecture, roads and garden art.The processing of river pebble is divided into three stages: coarse crushing of jaw crusher, medium crushing of impact crusher or cone crusher and sand making of sand making machine.
BASIC PROCESS OF PEBBLES SAND MAKING PLANT
The pebbles sand making process is divided into four stages: coarse crushing, medium fine crushing, sand making and sieving.
The first stage: coarse crushing
The pebbles blasted from the mountain is fed uniformly by the vibrating feeder through the silo and transported to the jaw crusher for coarse crushing.
The second stage: medium broken
The coarsely crushed materials are screened by vibrating screen and then conveyed by belt conveyor to cone crusher for medium crushing. The crushed stones are conveyed to the vibrating screen through a belt conveyor to sieve out different specifications of stones. The stones that meet the requirements of the customer’s particle size are conveyed to the finished product pile through the belt conveyor. The cone crusher crushes again, forming a closed circuit cycle.
The third stage: sand making
The crushed material is larger than the size of the two-layer screen, and the stone is conveyed to the sand maker machine through the belt conveyor for fine crushing and shaping.
The fourth stage: screening
The finely crushed and reshaped materials are screened by circular vibrating screen for coarse sand, medium sand and fine sand.
Note: For the sand powder with strict requirements, a sand washing machine can be added behind the fine sand. The waste water discharged from the sand washing machine can be recovered by the fine sand recycling device. On the one hand, it can reduce environmental pollution, and on the other hand, it can increase sand production.
The sand making production line has the features of reasonable configuration, high automation, low operation cost, high crushing rate, energy saving, environmental protection, high capacity and easy maintenance, the manufactured sand conforms to national standard for construction sand, uniform grain, excellent particle size, well graded.
The equipments of the sand making production line are configured in accordance with the specification and output as well as application of the sand, we provide solution and technical support, and design the process according to the production site of customer, we make every effort to provide the most reasonable and economic production line for customers.
Technical description:
1. This process is designed according to the parameters provided by the customer. This flow chart is for reference only.
2. The actual construction should be adjusted according to the terrain.
3. The mud content of the material cannot exceed 10%, and the mud content will have an important impact on the output, equipment and process.
4. SANME can provide technological process plans and technical support according to the actual requirements of customers, and can also design non-standard supporting components according to the actual installation conditions of customers.