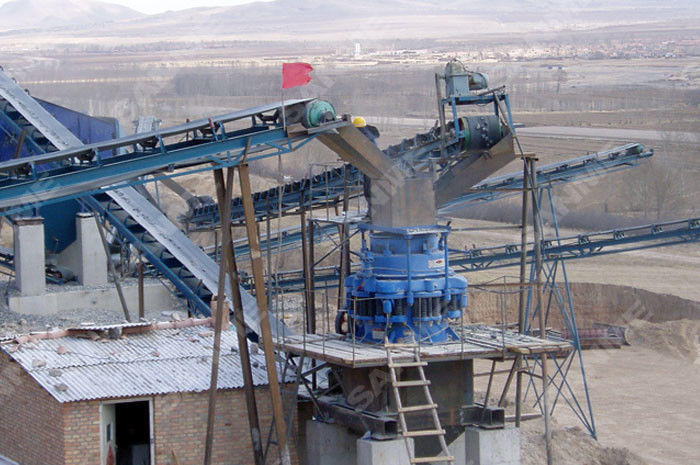
400Kw Metallurgy Feeding 460mm Cone Crusher Machine
2025-3-12
The common types of aggregate crushers mainly include the following:
1、 Squeezing crusher
Jaw crusher
Features: Simple structure, high reliability of continuous operation, low price, adjustable discharge port, small height difference required for equipment layout in the factory building.
Applicable scenario: In the coarse crushing stage, it is suitable for processing large materials such as granite, limestone, etc., which do not exceed 320MPa.
Advantages and disadvantages: The advantages are simple structure, sturdy and durable, and not easy to block; The disadvantage is that the lining plate is prone to wear and the product particle size distribution is uneven.
gyratory crusher
Features: Large processing capacity, high crushing ratio (6-9.5), suitable for hard and highly abrasive ores.
Applicable scenarios: rough crushing operations, especially in situations where the output exceeds 1000 tons/hour.
Advantages and disadvantages: The advantages are large processing capacity and uniform product granularity; The disadvantage is that the overall investment is high, the amount of civil engineering is large, and it is suitable for large-scale sand and gravel aggregate projects.
cone crusher
Characteristics: High crushing force, large crushing ratio (6-9.5), low energy consumption, and good adaptability to most materials, as well as materials with high hardness and difficult to crush.
Applicable scenarios: Intermediate and fine crushing operations, especially for the crushing of hard materials.
Advantages and disadvantages: The advantages are high output and reliable operation; The disadvantage is that the manufacturing and maintenance of the hydraulic system and the dynamic cone support structure are complex, and when used as fine crushing equipment, the product particle shape is poor and the powder content is low.
double-geared roller crusher
Characteristics: Crushing ratio of 5-8, crushed by squeezing or other methods.
Applicable scenarios: Suitable for brittle materials such as coal and limestone with a compressive strength not exceeding 160MPa, commonly used for medium and coarse crushing.
2、 Impact crusher
impact crusher
Features: High crushing ratio (20-50), low energy consumption, good finished particle size, easy to adjust discharge particle size.
Applicable scenarios: coarse, medium, and fine crushing of soft and medium hard materials.
Advantages and disadvantages: The advantages are high crushing efficiency and uniform product particle size; The disadvantage is that the hammer and impact plate are prone to wear and tear.
Hammer crusher
Features: crushing ratio of 10-25, high production capacity, simple operation and maintenance.
Applicable scenarios: Soft and medium hard materials with a compressive strength not exceeding 150MPa, such as limestone, coal, etc.
Advantages and disadvantages: The advantages are simple structure and high production capacity; The disadvantage is that it is not suitable for products with large particle sizes.
Vertical shaft crusher
Characteristics: The structural form is relatively simple, the crushing ratio is large, and the product particle shape is good.
Applicable scenarios: Fine crushing and sand making stage.
3、 Other types
In addition to the common crushers mentioned above, there are also some special types of crushers, such as roller crushers, rod mill crushers, etc., which also have certain application value in certain specific situations.
In summary, there are various types of common aggregate crushers, each with its own advantages, disadvantages, and applicable scenarios. When choosing, it is necessary to comprehensively consider factors such as material properties, production requirements, and investment budget to ensure the selection of the most suitable crusher type.