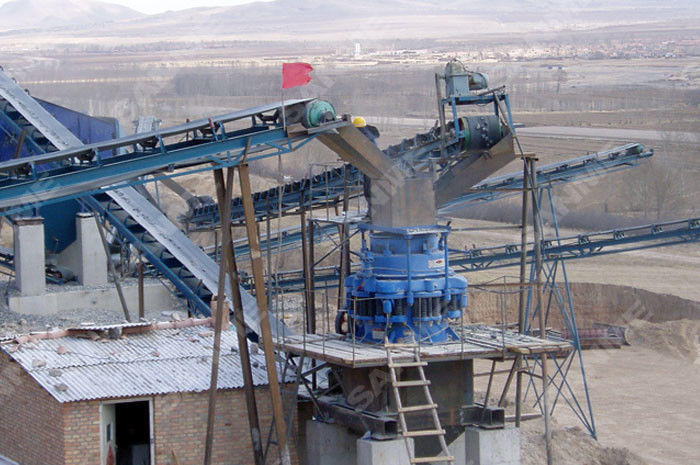
400Kw Metallurgy Feeding 460mm Cone Crusher Machine
2024-11-15
The sand and gravel production line may encounter a variety of common problems during operation, which involve various components of the equipment and process flows. The following is a summary and arrangement of these common problems:
1、Equipment failure
Cleaning screen failure
Wheat grains in the sand and gravel: The possible reason is that the internal damper of the stone discharge nozzle is small or the screen surface inclination is not appropriate. The solution is to adjust and increase the internal damper of the stone discharge nozzle, or adjust the screen surface inclination to a suitable position.
Too much crushed material: The possible reason is that the gap between the tooth plate and the screen of the crushing device is too small, the screen hole is too large or worn, or the bolts and wooden wedges are loose. The solution is to adjust the gap between the tooth plate and the screen, replace the worn screen hole, or tighten the bolts and wooden wedges.
Large vibration or shaking: The possible reason is that the bolts or connectors are loose. The solution is to check and tighten all connectors and bolts.
Grinding mill failure
The body shakes: The possible reason is that the bolts connecting the grinding head and the frame are loose. The solution is to tighten the connecting bolts.
No material or little material: The common reason is that the screen is blocked. The solution is to clean the screen.
Output decrease: Possible reasons are too large gap between rollers or worn teeth. The solution is to tighten the spring to ensure that the gap between the two ends of the roller is consistent, and repair or replace the worn teeth.
High material temperature: Possible reasons are serious wear of rollers or high machine temperature in summer. The solution is to repair or replace worn rollers, and stop the machine to dissipate heat during high temperatures in summer.
Motor failure
Too high temperature: Possible reasons are lack of oil, dirt entering the bearing, damage or motor overload. The solution is to add an appropriate amount of lubricating grease, clean the bearing, replace damaged bearings or lubricating grease, and avoid motor overload.
Spiral agitator failure
No material is discharged from the discharge port: Possible reasons are incorrect motor rotation, blockage of the discharge port or broken agitator blades. The solution is to check the motor rotation, clean the blockage of the discharge port, or replace the broken blades.
Agitator shaft does not rotate: Possible reasons are overfeeding, belt slippage or internal failure of the agitator. The solution is to reduce the feed amount, check and adjust the belt tension, or check the inside of the agitator and troubleshoot.
2、Process problems
Reduced processing capacity
Possible reasons are that the gaps between the screen bars are blocked by materials or the feeding is uneven. The solution is to suspend the operation of the equipment, clean the blockages in the gaps between the screen bars, and adjust the feeding mechanism to ensure uniform feeding.
Impacting sound inside the equipment
Possible reasons are that non-crushed objects enter the equipment, the lining fasteners are loose, the hammer hits the lining, or the hammer and other parts are broken. The solution is to check the tightness of the lining, adjust the space between the hammer and the screen bar, replace the broken parts, and add an appropriate amount of lubricating grease.
Large vibration
Possible reasons are broken hammer head, unbalanced rotor, bent or broken pin shaft, cracked triangular disk or disc, and loose anchor screws. The solution is to remove and replace the damaged hammer head, ensure that the static balance of the rotor meets the requirements; replace the broken pin shaft; repair or replace the triangular disk or disc with electric welding; tighten the anchor screws.
3、Safety and environmental issues
Safety issues
During the production of sand and gravel, there may be problems such as not considering the maintenance platform and maintenance equipment, and not setting up maintenance walkways, which may cause the equipment to be manually suspended and started, and the monitoring takes a lot of time and is prone to blockage and other failures, affecting the safety of workers. The solution is to consider installing maintenance equipment, laying special maintenance walkways, and setting up handrails or guardrails to ensure the safety of personnel.
Environmental issues
A large amount of flying dust and sewage will be generated during the production of sand and gravel, posing a threat to the environment and the health of workers. The solution is to equip environmental protection equipment such as dust collectors, spray equipment, fine sand recovery machines, and sewage sedimentation tanks to reduce the emission of pollutants.
In summary, the sand and gravel production line may encounter various problems during operation, and regular inspections and maintenance are required to promptly discover and solve problems to ensure the normal operation and efficient output of the production line. At the same time, it is also necessary to pay attention to safety and environmental issues, and take corresponding measures to ensure personnel safety and environmental protection.