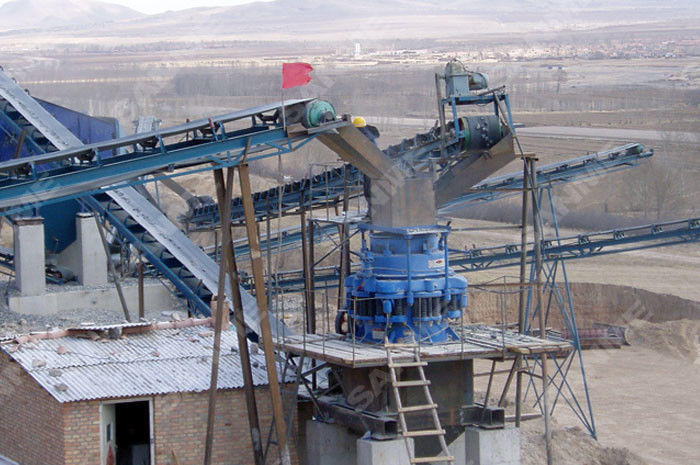
400Kw Metallurgy Feeding 460mm Cone Crusher Machine
2024-7-12
When choosing a granite crushing plant, multiple factors need to be considered comprehensively to ensure that the selected equipment can meet production needs and has good economic and practical performance. Here are some key selection steps and considerations:
1、 Clarify production requirements
Material properties: Granite is a material with high hardness, so it is necessary to choose crushing equipment that can handle high hardness materials.
Production demand: Determine the amount of material that needs to be processed per hour or per day in order to select a crushing station with appropriate production capacity.
Finished product particle size: Determine the required range of finished product particle size based on production requirements.
2、 Choose the appropriate type of crusher
According to the hardness and production requirements of granite, common types of crushers include jaw crushers, cone crushers, impact crushers, and hammer crushers. For high hardness materials such as granite, the following combinations are usually recommended:
Initial crushing stage: Jaw crusher, suitable for coarse crushing operations, can efficiently crush large granite blocks into smaller particles.
Intermediate and fine crushing stage: Cone crusher, suitable for intermediate and fine crushing of medium hardness and hard materials, can further refine particles and improve production efficiency.
3、 Determine the specific model and configuration
Model selection: After determining the type of crusher, it is necessary to choose the appropriate model based on production requirements and material characteristics. Different models of crushers have differences in processing capacity, crushing ratio, energy consumption, and other aspects.
Configuration plan: Determine the configuration plan for the crushing station based on the overall layout and process flow of the production line. For example, is it necessary to configure auxiliary equipment such as feeders, screening equipment, and conveyor belts.
4、 Consider other factors
Equipment quality: Choose manufacturers and brands with good quality reputation to ensure the stability and durability of the equipment.
Energy consumption and efficiency: Pay attention to the energy consumption and efficiency ratio of equipment, and choose high-efficiency and energy-saving equipment to reduce production costs.
After sales service: Consider the quality of the manufacturer’s after-sales service and the supply of accessories to ensure that the equipment can receive timely technical support and maintenance services during use.
Transportation and installation: Consider the convenience of transportation and installation of the crushing station, as well as whether additional site preparation and infrastructure construction are required.
5、 Case analysis
Taking the granite crushing production line with an hourly output of 800 tons as an example, its configuration plan may include:
Main equipment: PE1200 * 1500 jaw crusher (primary crushing), HST315S single cylinder hydraulic cone crusher (medium fine crushing), HPT300C multi cylinder hydraulic cone crusher (fine crushing), etc.
Auxiliary equipment: feeders, screening equipment, conveyor belts, etc.
This configuration scheme can ensure the efficient and stable operation of the production line, and meet the production needs of high output and high quality.
In summary, when choosing a granite crushing plant, it is necessary to comprehensively consider multiple factors such as production demand, crusher type, specific model and configuration, equipment quality, energy consumption and efficiency, after-sales service, transportation and installation. Through a scientific and rational selection process, it can be ensured that the selected equipment can meet production needs and has good economic and practical performance.