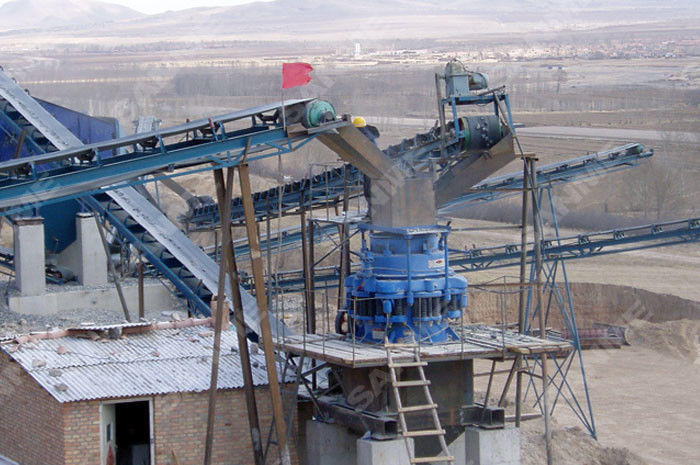
400Kw Metallurgy Feeding 460mm Cone Crusher Machine
2024-5-9
The working principle of a impact crusher is based on the impact between materials for crushing. The following is its detailed working principle:
Drive and rotation: The electric motor of the impact crusher drives the rotor to rotate at high speed through a transmission system (such as triangular tape).
Feed: The material to be crushed enters the crusher from the feed inlet, usually located above the rotor.
First crushing: When the material enters the range of rotor rotation, it will first be impacted by the hammer on the rotor plate. These plate hammers are in a radial state under the action of centrifugal force, and perform the initial crushing of the material.
Counterattack crushing: After the initial crushing, the material is thrown towards the counterattack board along the tangent direction of the plate hammer rotation. The material collided with the impact plate and further shattered.
Repeated crushing: The crushed material returns from the impact plate to the space where the hammer rotates and enters the next crushing cycle. This process may go through multiple cycles of “plate hammer counterattack plate” until the material is crushed to the desired particle size.
Discharge: When the material is crushed to a particle size smaller than the required crushing size, it is discharged from the machine along the gap between the plate hammer and the impact plate, becoming the crushed product.
Throughout the entire working process, the impact crusher crushes materials through high-speed relative motion between the plate hammer and the impact plate. The materials are subjected to multiple impacts and compressions in the crushing chamber, resulting in the required particle size. Meanwhile, the special structural design inside the crusher can effectively disperse and absorb impact energy, reducing the wear and failure rate of the machine.
The advantages of a counterattack crusher are mainly reflected in the following aspects:
High crushing efficiency: The impact crusher uses a high-speed rotating rotor to drive the plate hammer to crush the material, while utilizing the material’s own impact force for impact crushing. The crushing efficiency is high and it can quickly process a large amount of material.
High crushing ratio: The crushing ratio of the impact crusher is relatively high, which can crush materials to smaller particle sizes at once, reducing the number and energy consumption of subsequent processing equipment.
Uniform particle size of finished products: The impact crusher adopts a design of multi-stage crushing and multi-stage impact, which can fully crush and disperse materials in the crushing chamber, thereby obtaining more uniform particle size and more regular shape of finished products.
Strong adaptability: The impact crusher is suitable for handling materials with various hardness, such as limestone, gypsum, coal, etc., and can adapt to the crushing needs of materials with different particle sizes by adjusting the gap between the impact plate and the hammer.
Easy to maintain and upkeep: The structure of the impact crusher is relatively simple, making it easy to maintain and upkeep. Meanwhile, the vulnerable parts such as the hammer and impact plate are made of wear-resistant materials, which have a long service life and can reduce equipment maintenance costs.
Excellent environmental performance: The impact crusher generates relatively low dust and noise during the crushing process, which meets environmental requirements. At the same time, the crushing process does not produce pollutants such as wastewater and exhaust gas, and has no pollution to the environment.
In summary, the impact crusher has advantages such as high crushing efficiency, large crushing ratio, uniform product particle size, strong adaptability, easy maintenance and upkeep, and excellent environmental performance. Therefore, it has been widely used in industries such as mining, construction, and metallurgy.