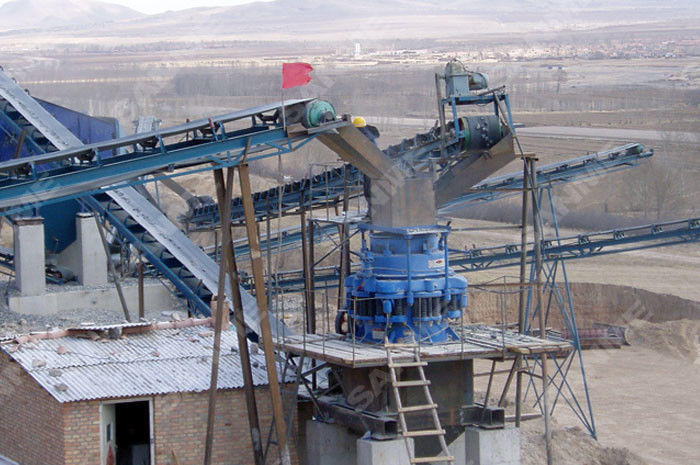
400Kw Metallurgy Feeding 460mm Cone Crusher Machine
2024-5-7
When planning the equipment selection and configuration of the stone crushing plant, multiple factors need to be comprehensively considered to ensure the efficient and stable operation of the production line. Here are some key planning steps:
Requirement analysis:
Determine the target production capacity, product quality requirements, and raw material characteristics (such as hardness, humidity, particle size distribution, etc.) of the production line.
Evaluate the operating costs of the production line, including equipment procurement costs, maintenance costs, energy consumption, etc.
Equipment selection:
Crusher: Select the appropriate type of crusher based on the hardness and particle size distribution of the raw materials. For example, for hard materials, a jaw crusher or a cone crusher is a better choice; For medium hard or soft materials, a impact crusher may be more suitable.
Screening machine: Select a suitable screening machine according to the product particle size requirements to ensure product quality.
Feeder: Ensure that the feeder can evenly and continuously feed raw materials into the crusher, avoiding equipment damage or reduced production efficiency caused by uneven feeding.
Conveyor: Choose a belt conveyor or other type of conveyor that is suitable for the scale and transportation needs of the production line.
Equipment configuration:
Crushing process: Design a reasonable crushing process based on the characteristics of raw materials and product requirements. For raw materials with higher hardness or larger particle size, multi-stage crushing may be necessary; For medium hard or soft materials, single stage crushing can be used.
Equipment quantity: Determine the required number of equipment based on the target production capacity of the production line and the processing capacity of the equipment. Ensure that the number of equipment can meet production needs without causing resource waste.
Equipment layout: Reasonably plan the layout of equipment to ensure smooth connection between equipment, smooth material flow, and reduce the residence time of materials on the production line.
Environmental and safety considerations:
When selecting equipment, priority should be given to equipment with low noise, low dust, and low energy consumption.
Equip necessary dust removal equipment, noise reduction equipment, and wastewater treatment equipment to ensure that the production line meets environmental standards.
Strengthen the safety protection measures of equipment to ensure the safety of operators.
Intelligence and automation:
Consider introducing intelligent and automation technologies, such as intelligent control systems, remote monitoring systems, etc., to improve the automation level and operational efficiency of the production line.
Maintenance and upkeep:
When selecting equipment, consider the maintenance cost and ease of maintenance of the equipment.
Develop a reasonable maintenance plan to ensure the long-term stable operation of the equipment.
Backup and redundancy design:
For critical equipment, consider setting up backup or redundant devices to cope with possible equipment failures or maintenance needs.
Cost benefit analysis:
After the equipment selection and configuration are completed, a cost-benefit analysis is conducted to ensure that the selected equipment and configuration scheme have a high cost-effectiveness.
In summary, when planning the equipment selection and configuration of the gravel crushing production line, multiple factors need to be comprehensively considered to ensure the efficient, stable, environmentally friendly, and safe operation of the production line.